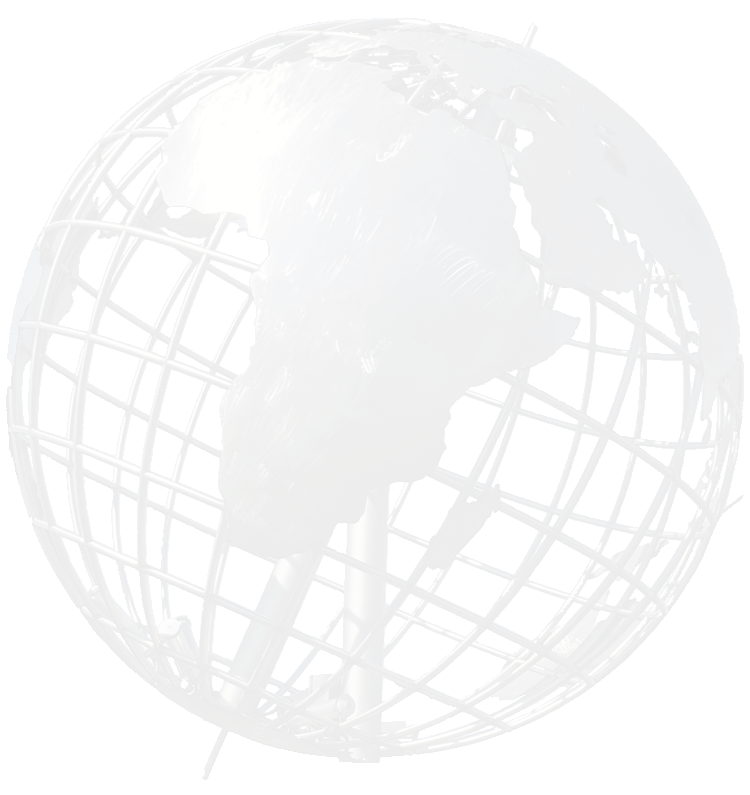
Einfluss wichtiger Legierungs- und Spurenelemente auf die Eigenschaften in nichtrostenden Stählen
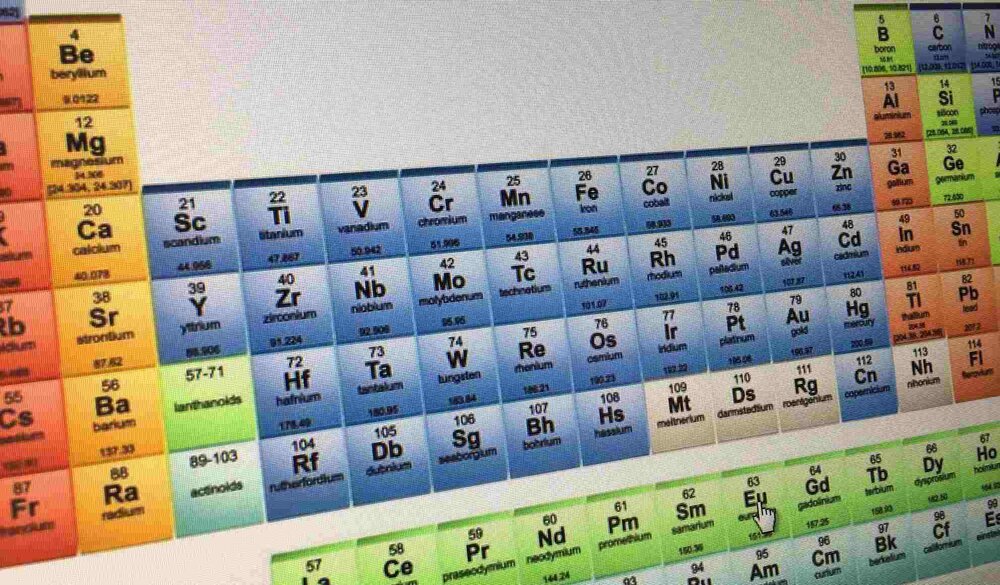
Nichtrostende Stähle
Im Jahr 1912 wurde die Korrosionsbeständigkeit von nichtrostenden Stählen durch die Entwicklung des V2A Stahls entdeckt. Hierbei wurde festgestellt, daß die Kombination der Elemente Chrom und Nickel in Verbindung mit einer abgestimmten Wärmebehandlung ein Optimum an Korrosionsbeständigkeit und zugleich gute mechanische Eigenschaften bewirkt. Die damals aus V für Versuch und A für Austenit gebildete Bezeichnung V2A stand für Chrom-Nickel-Stahl. Sie wird nach wie vor als Synonym für Edelstahl Rostfrei verwendet.
Chromgehalte von mehr als 10,5 % bewirken die Bildung einer dünnen, dichten, festhaftenden Passivschicht aus Chromoxid. Mit höherem Chromgehalt und Zugabe von Nickel und Molybdän wird die Passivschicht kompakter und die Korrosionsbeständigkeit in wässrigen Medien als auch die Beständigkeit in Säuren deutlich erhöht.
Wirkungsweise von Legierungs- und Spurenelementen auf die Eigenschaften von nichtrostenden Stählen
Die nichtrostenden Stähle erhalten durch ihre Legierungs- und Spurenelemente die grundlegenden Eigenschaften, die für den Einsatz erforderlich sind. Im Zusammenwirken mit dem Umwandlungsverhalten werden die Gebrauchs- und Verarbeitungseigenschaften durch die Legierungselemente eingestellt.
Die mechanischen Eigenschaften wie die Härte, Dehngrenze, Zugfestigkeit, Dehnung und Kerbschlagzähigkeit können infolge der unterschiedlichen Einflüsse der Legierungselemente gezielt auf den Bedarf angepasst werden.
Thermische Eigenschaften des nichtrostenden Stahls sowie hohe Beständigkeit gegen Materialabtrag durch Verschleiß und chemische oder thermische Korrosion können ebenfalls durch gezielte Legierungsmaßnahmen eingestellt werden. Die wesentlichen Legierungselemente und deren Wirkungsweise sind im folgendem alphabetisch aufgeführt:
- Aluminium Al
Aluminium Al
Aluminium wird den nichtrostenden Stählen ähnlich wie Silizium zur Abbindung des im Stahl gelösten Sauerstoffs in Form von Aluminiumoxid zugesetzt. Übliche Gehalte liegen dabei unter 0,1 %.
Bei hitzebeständigen ferritischen Stählen verbessert Aluminium die Zunderbeständigkeit durch Bildung festhaftender Aluminiumoxidschichten. Diese verzögern den Verzunderungsprozess unter Einwirkung oxidierender Gasatmosphären. Übliche Aluminiumgehalte der ferritischen hitzebeständigen Stähle betragen zwischen 0,5 und 2,0 %.
Ferritbildner
Desoxidationsmittel
- Chrom Cr
Chrom Cr
Chrom ist als Hauptlegierungselement ursächlich für die Korrosionsbeständigkeit der nichtrostenden Stähle. Deshalb sind definitionsgemäß nichtrostende Stähle solche, die mit mindestens 10,5 Masse-% Chrom legiert sind. In der Tat führt das Legierungselement Chrom in diesem Mindestanteil zur Ausbildung einer sehr dünnen, aber fest haftenden und bei Verletzung auch selbst heilenden sogenannten Passivschicht, die das darunter liegende Metall vor dem Angriff durch die umgebenden Medien schützt. So ist beispielsweise für die gebräuchlichen ferritischen nichtrostenden Stähle 1.4003 und 1.4512 nur der Mindest-Chromgehalt von 10,5 % vorgegeben.Ferritbildner
Legierungselement
Die traditionelle Namensgebung „Nichtrostende Stähle“ hat ihren Ursprung darin, dass diese Werkstoffe bei Auslagerung an normaler Atmosphäre nicht rosten. Sie bedeutet aber nicht, dass diese Werkstoffe beliebigen Medien ohne Korrosionserscheinungen ausgesetzt werden können. Um eine für vielfältigere Korrosionsbeanspruchung ausreichende Beständigkeit zu erzielen, muss ein höherer Chromgehalt als der eingangs genannte Mindestgehalt von 10,5 % vorgesehen werden. Deshalb weist der ferritische nichtrostende Stahl 1.4510 einen Mindest-Chromgehalt von 16,0 %, der austenitische nichtrostende Standardstahl 1.4301 einen solchen von 17,0 % auf. Ganz allgemein kann man davon ausgehen, dass die Beständigkeit der nichtrostenden Stähle gegen Loch- und Spaltkorrosion in chloridhaltigen Medien linear mit ihrem Chromgehalt zunimmt, wie die hierfür als maßgeblich angesehene Wirksumme W aussagt.
Mit zunehmendem Chromgehalt verbessert sich auch die Beständigkeit der nichtrostenden Stähle gegenüber stark oxidierenden Säuren (beispielsweise Salpetersäure), wobei der Chromgehalt der austenitischen nichtrostenden Stähle bis herauf zu rund 33 % gesteigert
werden kann, wie das Beispiel des austenitischen nichtrostenden Stahls 1.4591 zeigt. Ein höherer Chromgehalt verbessert die Hitze- und Zunderbeständigkeit nichtrostender Stähle. So ist Chrom ein wichtiges Legierungselement zur Erhöhung der Zunderbeständigkeit von
Edelstahl Rostfrei gegenüber heißen oxidierenden Gasen bis herauf zu etwa 1150 °C. Deshalb ist der Werkstoff 1.4845 mit rund 25 % Chrom ein häufig verwendeter hitzebeständiger Werkstoff.Mit steigendem Chromgehalt wird sowohl die 0,2 %-Dehngrenze als auch die Zugfestigkeit erhöht. Gleichzeitig sinkt die Bruchdehnung als Maß für das Umformvermögen des Werkstoffs mit steigendem Chromgehalt.
- Kohlenstoff C
Kohlenstoff C
Kohlenstoff ist aufgrund seines sehr kleinen Atomradius im Regelfall auf Zwischengitterplätzen im Atomgitter gelöst. Sein Gehalt wird mit Ausnahme der martensitischen Stähle möglichst niedrig gehalten. In der Praxis wird sowohl bei ferritischen als auch austenitischen Güten ein
Kohlenstoffgehalt unter 0,03 % angestrebt (sogenannte „Extra Low Carbon-“ bzw. ELC-Güten).Kohlenstoff begünstigt bei erhöhter Temperatur die Bildung von Chromkarbiden, die sich bevorzugt auf den Korngrenzen ausscheiden. Dies führt zu einer Versprödung des Werkstoffs und gegebenenfalls auch zu einer Sensibilisierung für interkristalline Korrosion. Ein niedriger Kohlenstoffgehalt reduziert deshalb die Neigung zur Sensibilisierung und interkristallinen Korrosion des Werkstoffs.
Austenitbildner
Legierungselement für martensitische Stähle
Alternativ kann der Kohlenstoff auch durch Zulegieren der sogenannten Stabilsierungselemente Titan und /oder Niob als Titankarbid oder Titankarbonitrid sowie Niobkarbid abgebunden werden.
Im gelösten Zustand erhöht Kohlenstoff die 0,2 %-Dehngrenze und die Zugfestigkeit, während gleichzeitig die Bruchdehnung als Maß für das Umformvermögen sinkt.
Nur bei den martensitischen nichtrostenden Stählen ist der Kohlenstoff mit Gehalten bis zu 0,7 % ein nützliches Legierungselement, welches zur Härtbarkeit des Werkstoffs beiträgt. Die erreichbare Härte zum Beispiel für Schneidwaren und technische Messer steigt dabei mit steigendem Kohlenstoffgehalt an. Gleichzeitig verringert ein hoher Kohlenstoffgehalt aber auch die Duktilität des Werkstoffs, etwa im Vergleich zu austenitischen nichtrostenden Stählen.
- Kupfer Cu
Kupfer Cu
Kupfer ist bei den nichtrostenden Standardstählen lediglich Spurenelement und wird über den Schrott in die Schmelze eingetragen. Als Spurenelement ist Kupfer häufig auf einen maximalen Wert von 0,5 % begrenzt. Reale Kupfergehalte betragen bei Austeniten etwa 0,2 bis 0,4 %.Dem Kupfer als Legierungselement in chemisch beständigem Edelstahl Rostfrei gilt das besondere Interesse im Hinblick auf die Korrosionsbeständigkeit in sauren, nichtoxidierenden Medien, u. a. in Schwefelsäure und Phosporsäurelösungen. Ein bewährtes Beispiel hierfür ist der Werkstoff 1.4503 mit 2,5 bis 3,5 % Kupfer. Technische Bedeutung haben darüber hinaus insbesondere der Werkstoff 1.4539 mit einem Kupfergehalt zwischen 1,2 bis 2,0 % sowie der Werkstoff 1.4529 mit einem Kupfergehalt zwischen 0,5 und 1,5 %.
Austenitbildner
in der Regel nur Spurenelement
Kupfer wird sowohl zur Verbesserung des Kaltstauchverhaltens als auch der Korrosionsbeständigkeit zulegiert. Ein bewährtes Beispiel für eine spezielle Ausführung von Edelstahl Rostfrei mit verbesserter Kaltstauchbarkeit infolge verminderter Kaltverfestigung durch Zusatz von Kupfer bis herauf zu 4 % ist der Werkstoff 1.4567. Mit der Verbesserung des Kaltstauchverhaltens verbessert sich auch die Prägbarkeit für Schmuck, Medaillen und Münzen.
Bei ausscheidungsgehärtetem nichtrostenden Stahl (PH-Stahl) bewirkt Kupfer in einer kontrollierten Wärmebehandlung ein Ausscheidungshärten, welches die Festigkeit des Werkstoffs erheblich erhöht. Ein bewährtes Beispiel hierfür ist der Werkstoff (1.4542) mit 3,0 bis 5,0 % Cu.
- Mangan Mn
Mangan Mn
Mangan ist ebenso wie Nickel ein Austenitbildner und wird in den Standardstählen in einem Gehalt bis zu 2 % zulegiert. Mangan erschwert in austenitischen Chrom- Nickel-Stählen die Umwandlung des Austenits in Martensit bei der Umformungs- oder Tieftemperaturbeanspruchung.Mangan hat keinen erkennbaren Einfluss auf die Korrosionsbeständigkeit. In Verbindung mit Schwefel bilden sich Mangansulfide, welche die Beständigkeit des Werkstoffs gegenüber Lochkorrosion erheblich vermindern.
Austenitbildner
Legierungselement
Aus Kostengründen kann Mangan auch zur Substitution des teuren Legierungselements Nickel zulegiert werden (sogenannte Manganaustenite). Der Mangangehalt dieser Werkstoffe beträgt dann zwischen 5,0 und 10,5 %. Beispiele hierfür sind die Werkstoffe 1.4371, 1.4372 und 1.4376. Die Manganaustenite haben insbesondere im asiatischen Raum eine große wirtschaftliche Bedeutung für Standard-Haushaltartikel wie Kochtöpfe usw.
Mangan erhöht die Löslichkeit des Austenits für Stickstoff als Legierungselement. Beispiele hierfür sind der austenitische Werkstoff 1.4565 oder auch der ferritisch-austenitische Duplexstahl 1.4162. - Molybdän Mo
Molybdän Mo
Molybdän ist nach Chrom das wichtigste Legierungselement für die Korrosionsbeständigkeit der nichtrostenden Stähle. Insbesondere in nicht oxidierenden Säuren wie Schwefelsäure, Ameisensäure etc. erhöht Molybdän die Beständigkeit nichtrostender Stähle gegen allgemeine Flächenkorrosion. In chloridhaltigen Medien erhöht Molybdän die Beständigkeit gegenüber Loch- und Spaltkorrosion. In der hierfür als maßgeblich angesehenen Wirksumme W wird der Molybdängehalt deshalb mit dem Faktor 3,3 berücksichtigt. Molybdän wirkt demnach deutlich stärker als Chrom auf die Lochkorrosionsbeständigkeit.Ferritbildner
Legierungselement
Molybdän hat eine starke Neigung zur Seigerung. Aus diesem Grund sind die Legierungsgehalte üblicherweise auf maximal 6 % begrenzt. Eine weitere Erhöhung des Molybdängehalts würde keine weitere Verbesserung in der Lochkorrosionsbeständigkeit erbringen.
Molybdän verbessert zugleich die Beständigkeit gegenüber Spannungsrisskorrosion und steigert die Warmfestigkeit. Unter den zahlreichen Beispielen für molybdänlegierte nichtrostende Stähle sind die Werkstoffe 1.4404, 1.4571, 1.4462, 1.4529 und 1.4562 zu nennen.
Ebenso wie Chrom erhöht auch Molybdän die 0,2 %- Dehngrenze und die Zugfestigkeit. Gleichzeitig sinkt mit steigendem Molybdängehalt die Bruchdehnung als Maß für die Umformbarkeit des Werkstoffs.
- Nickel Ni
Nickel Ni
Nickel ist neben Chrom und Molybdän das bedeutendste Legierungselement für austenitische nichtrostende Stähle. Nickel ist ein Austenitbildner und erweitert den Zustandsbereich des Austenits in Abhängigkeit von der Höhe des Legierungsgehaltes bis weit unter Raumtemperatur, wodurch der nichtrostende Stahl duktiler wird.Bei austenitischen nichtrostenden Stählen liegt der Nickelgehalt etwa zwischen 8 und 26 %, bei nichtrostendem Duplexstahl meist zwischen 2 und 7 % und bei ferritischen Güten in der Regel bei maximal 2 %. Korrosionstechnisch trägt Nickel kaum zu einer höheren Beständigkeit des nichtrostenden Stahls gegen allgemeine Lochkorrosion in chloridhaltigen wässrigen Medien bei.
Austenitbildner
Legierungselement
Nickel ist deshalb auch nicht in der Formel für die Wirksumme enthalten. Nickel wirkt sich allerdings positiv auf das Repassivierungsverhalten aus und reduziert auch die Geschwindigkeit eines Angriffs durch Lochkorrosion. Nickel ist maßgeblich für die Korrosionsbeständigkeit von Edelstahl Rostfrei gegenüber nichtoxidierenden Säuren. Bei Hochtemperaturanwendungen sollten hoch nickelhaltige Legierungen in reduzierenden, sulfidierenden Umgebungen vermieden werden, um die Bildung von niedrigschmelzendem Nickelsulfid zu verhindern.
Im Vergleich zu Standardausteniten mit näherungsweise 10 % Nickel, wo das Minimum der Spannungsrisskorrosionsbeständigkeit des Werkstoffs liegt, weisen sowohl nickelarme Güten wie 1.4462 als auch nickelreiche Qualitäten wie 1.4539 einen erhöhten Widerstand gegen
Spannungsrisskorrosion auf.Nickel wirkt der Bildung von Verformungsmartensit bei einer Umformung, zum Beispiel durch Tiefziehen entgegen. Für kritische Umformvorgänge hat sich deshalb der Einsatz höher nickelhaltiger Legierungsvarianten bewährt. Für anspruchsvolle Tiefziehteile mit Mehrfachzug wie zum Beispiel Kugelschreiberminen und Batteriehülsen wird deshalb der austenitische nichtrostende Stahl 1.4303 mit einem Nickelgehalt von 12 % bevorzugt verwendet.
- Niob Nb
Niob Nb
Um die negativen Wirkungen von Kohlenstoff zu reduzieren, wird dem nichtrostenden Stahl als Stabilisator unter anderem Niob zugesetzt. Niob zeigt eine größere Neigung zur Karbidbildung als Chrom und wirkt ähnlich wie Titan als Kohlenstoffbinder. Niob reduziert dadurch die
Sensibilisierung und Neigung zu interkristalliner Korrosion.Im Vergleich zu Titan hat Niob sogar noch eine stärkere kohlenstoffbindende Wirkung und erhöht ebenso die Fließspannung des nichtrostenden Stahls und damit dessen Festigkeit, insbesondere bei höheren Temperaturen.
Ferritbildner
Stabilisierungselement
Da Titankarbide von stark oxidierenden Säuren wie Salpetersäure angegriffen werden können und aufgrund dessen es zu interkristalliner Korrosion kommen kann, wird eine Niobstabilisierung gegenüber einer Titanstabilisierung in manchen nichtrostenden Stählen bevorzugt. Einige ferritische nichtrostende Stähle wie zum Beispiel 1.4509 und 1.4521 weisen auch eine Doppelstabilisierung mit Titan und Niob auf.
Bei ferritischem nichtrostenden Stahl gewährleistet Niob eine feinkörnige Struktur beim Schweißen, die einer Versprödung insbesondere beim MIG-Schweißen entgegenwirkt. Da Niob ähnlich wie Titan den Austenitbildner Kohlenstoff bindet, wirkt es zudem als Ferritstabilisator.
- Schwefel S
Schwefel S
Bei den meisten nichtrostenden Güten steht die Korrosionsbeständigkeit im Vordergrund, bei ihnen ist der Schwefelgehalt daher normgemäß auf max. 0,015 oder sogar 0,010 % begrenzt. Die moderne Stahlwerkstechnologie erlaubt darüber hinaus in vielen Fällen eine weitergehende
Reduzierung auf typische Werte von unter 0,005 %.Schwefel wirkt sich ungünstig auf die Korrosionsbeständigkeit, zum Beispiel in chloridhaltigen wässrigen Medien aus. Auch das Umformverhalten wird durch höhere Schwefelgehalte negativ beeinflußt. Ebenso wirkt sich ein höherer Schwefelgehalt auch ungünstig auf die Kerbschlagzähigkeit aus.
in der Regel Spurenelement
Legierungselement für Automatenstähle
Einen positiven Einfluß hat Schwefel jedoch auf das Zerspanungsverhalten, zum Beispiel durch Drehen oder Fräsen. Für Produktformen, die üblicherweise einer zerspanenden Bearbeitung unterliegen, dürfen einige nichtrostende Stahlgüten leicht angehobene Schwefelanteile von
typischerweise 0,015 bis 0,030 % aufweisen. Diese geringfügig erhöhten Schwefelanteile führen nur zu verhältnismäßig geringen Einbußen in der Korrosionsbeständigkeit.Sofern das Zerspanungsverhalten bei der Verarbeitung im Vordergrund steht, kann man auch die sogenannten Automatenstähle mit Schwefelgehalten von 0,15 bis 0,35 % verwenden. Diese Werkstoffe haben eine eigene Werkstoffnummer wie zum Beispiel 1.4305. Sie sind allerdings in ihrer Korrosionsbeständigkeit deutlich ungünstiger einzustufen als die schwefelarmen Vergleichswerkstoffs mit ähnlichem Chrom- und Nickelgehalt. Schwefelhaltige Automatenstähle wie der Werkstoff 1.4305 sind aufgrund ihrer ungünstigeren Korrosionsbeständigkeit für manche Anwendungsgebiete wie die Nahrungsmittelindustrie nicht zugelassen. Ebenso sind sie ungeeignet für Gegenstände mit lang andauerndem Hautkontakt wie Schmuck, Armbanduhren usw.
- Silizium Si
Silizium Si
Silizium ist eines der sogenannten Desoxidationselemente und wird dem Stahl zur Abbindung des gelösten Sauerstoffs in Form von Siliziumoxid zugesetzt. Übliche Gehalte an Silizium liegen unter 1,0 %.
Nichtrostende Stähle für Hochtemperaturanwendungen sind so aufgebaut, dass sie schützende Zunderschichten bilden können. Silizium wirkt hier sehr ähnlich wie Chrom. Es oxidiert selektiv und kann, sofern in ausreichender Menge vorhanden, durchgehende, stabile Schichten aus SiO2 bilden.Ferritbildner
Desoxidationselement
So verbessert Silizium die Zunderbeständigkeit und ist deshalb beispielsweise im hitzebeständigen austenitischen Werkstoffen wie 1.4828 und 1.4841 mit 1,5 bis 2,5 % zulegiert. Höhere Siliziumgehalte verbessern bei bestimmten Beanspruchungen auch die Korrosionsbeständigkeit gegenüber wässrigen Medien, z.B. gegenüber hochkonzentrierter Schwefel- oder Salpetersäure. Ein Beispiel hierfür ist der austenitische nichtrostende Stahl 1.4361 mit 3,7 bis 4,5 % Silizium.
Nichtrostende Stähle mit höheren Gehalten an Silizium sind nur bedingt zum Elektropolieren geeignet, falls hohe Ansprüche an das Oberflächenaussehen und die Glätte bestehen. - Stickstoff N
Stickstoff N
Stickstoff ist ebenso wie Kohlenstoff aufgrund seines sehr kleinen Atomradius auf Zwischengitterplätzen im Atomgitter angeordnet. Die maximale Löslichkeit in austenitischen Stählen beträgt 0,25 %. Sie kann insbesondere durch höhere Mangangehalte noch weiter erhöht werden.
Stickstoff ist ein starker Austenitbildner. In austenitischen nichtrostenden Stählen erhöht Stickstoff ähnlich wie Nickel die Stabilität des Austenits gegenüber verformungsinduzierter Martensitbildung. Gleichzeitig erhöht Stickstoff die 0,2 %- Dehngrenze, ohne gleichzeitig die Bruchdehnung signifikant zu vermindern. Bei Hochtemperaturanwendungen verbessert ein höherer Stickstoffgehalt die Kriechfestigkeit des Werkstoffs.Austenitbildner
Legierungselement
Stickstoff ist in den höher legierten, chemisch beständigen Stählen zugleich von bedeutendem Einfluss auf die Beständigkeit gegenüber Lochkorrosion. In die hierfür als maßgeblich angesehene Wirksumme W kann er deshalb mit dem Faktor 16 (Duplexstähle) oder 30 (hoch legierte Austenite) einbezogen werden. Beispiele sind die Werkstoffe 1.4462 mit 0,10 bis 0,22 % N, 1.4529 und 1.4562 mit 0,15 bis 0,25 % N, 1.4565 mit 0,3 bis 0,6 % N und 1.4591 mit 0,35 bis 0,60 % N.
In Duplexstählen wie 1.4362 und 1.4462 erweitert Stickstoff das Zweiphasengebiet Ferrit-Austenit und begünstigt damit die gewünschte Ausbildung des Duplexgefüges mit einem Volumenanteil von 50 % Ferrit und 50 % Austenit. Die Stickstoffgehalte der Duplexstähle liegen deshalb bevorzugt an der Obergrenze der Normvorgabe.
- Titan Ti
Titan Ti
Nichtrostende Stähle mit relativ hohen Kohlenstoffgehalten neigen zur Bildung von Chromkarbiden, hauptsächlich entlang der Korngrenzen. Diese sogenannte Sensibilisierung entsteht hauptsächlich nach dem Schweißen oder nach einer Hochtemperaturumformung und führt aufgrund der chromverarmten Zonen zu interkristalliner Korrosion.Titan zeigt eine größere Neigung zur Karbidbildung als Chrom und reagiert bevorzugt mit Kohlenstoff zu Titankarbid und Stickstoff zu Titankarbonitrid, so dass sich keine Chromverarmung in titanlegierten (stabilisierten) nichtrostenden Stählen ausbildet und eine gleichmäßige stabile Oxidschicht erhalten bleibt.
Ferritbildner
Stabilisierungselement
Die Bildung von Titankarbiden und Titankarbonitriden im Gefüge führt durch den Mischkristall verfestigenden Effekt zu erhöhten Härten und reduziert die Kerbschlagzähigkeit, Duktilität und Zerspanbarkeit des nichtrostenden Stahls. Beim Schweißen können titanstabilisierte Stähle in Kombination mit stickstoffhaltigem Spülgas zu gelblichen Schweißnähten führen. Zudem sind titanstabilisierte Stähle für das mechanische Hochglanzpolieren nicht geeignet, weil die Anwesenheit von Titankarbiden und Titankarbonitriden im Gefüge zur Bildung von
Titanschlieren auf der Oberfläche führt.Der Einsatz titanstabilisierter nichtrostender Stähle ist dann gerechtfertigt, wenn eine höhere Anwendungstemperatur von über 300 °C bis etwa 400 °C vorliegt. Im Vergleich zu nicht stabilisierten Güten erreichen die stabilisierten Werkstoffe dann eine höhere Warmdehngrenze und Warmzugfestigkeit im Vergleich zu den nicht stabilisierten Vergleichswerkstoffen wie zum Beispiel den ELC-Güten 1.4307 oder 1.4404. Zudem wird Titan bei ferritischen nichtrostenden Stählen gerne als Stabilisator verwendet, um ein unerwünschtes Kornwachstum und die damit einhergehende Versprödung des Stahls zu vermeiden.
- Vanadium V
Vanadium V
Vanadium wird den härtbaren martensitischen nichtrostenden Chromstählen zur Karbidbildung in geringen Mengen zulegiert, um den Werkstoff gegen Überhitzung unempfindlich zu machen. Beispiele hierfür sind die Werkstoffe 1.4110 und 1.4116 mit Vanadiumgehalten von etwa 0,15 %. Die Warmfestigkeit wird durch Vanadium signifikant erhöht.
Ferritbildner
in der Regel Spurenelement